Заправка холодильного оборудования фреоном
07.11.2018
Первый признак утечки хладагента – снижение холодопроизводительности агрегата. Работа компрессора не останавливается, но оборудование перестает морозить. Распознать утечку фреона можно по следующим признакам:
- повышенным температурным показателям в холодильной камере;
- беспрерывной работе компрессора без отключений;
- холодному конденсатору оборудования;
- образованию толстого слоя льда на задней стенке холодильника.
Для устранения возникшей проблемы необходимо обнаружить участок, на котором произошла утечка, ликвидировать не герметичность, заменить фильтр-осушитель, ведь параллельно с воздушными массами в холодильный контур проникает водяной пар, отвакуумировать агрегат и заправить его хладагентом. При проведении данных процедур следует воспользоваться течеискателем, вакуумным насосом и заправочным коллектором.
Как определить место утечки
Пропускание холодильного агента может быть замечено на паянных швах. Также возможна утечка вследствие возникновения механических повреждений трубопровода при перевозке или неисправностей испарителя при очистке испарителя от ледяного налета во времяразморозки. Также хладагент может вытекать на запененном участке – контурах трубопровода низкого и высокого давления, скрытых в теплоизоляции оборудования.
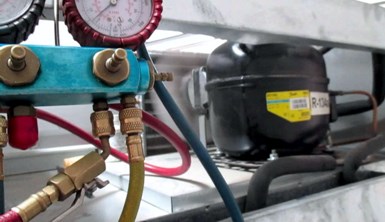
Ликвидация утечки
Процесс устранения проблемы состоит из нескольких этапов:
- подготовки места для пайки – его изоляции прокладкой из асбеста, во избежание повреждения узлов холодильника при использовании горелки;
- запайки участков, на которых обнаружена утечка фреона, с применением грелки, паяльной пасты и припоя на основе серебра;
- контрольной проверки оборудования с использованием течеискателя, в случае обнаружения утечек, их требуется устранить, а затем убедиться, что все сделано верно.
Заправка холодильной техники фреоном подразумевает:
- покупку требуемого хладагента;
- состыковку заправочной трубки с патрубком компрессора;
- спайку швов между заправочной трубкой и компрессором – пламя горелки не должно попадать во внутреннюю часть патрубка, так как это может повлечь за собой поломку компрессорного агрегата;
- устранение заглушки с фильтра-осушителя, установку фильтра на конденсатор и вставку в него капиллярной трубки;
- спайку швов фильтра;
- надевание на заправочную трубку клапанной полумуфты;
- проверку гладкости и ровности швов;
- подключение к муфте вакуума, проведение первичного вакуумирования оборудования до требуемого давления 64 Па.
Если ранее оборудование работало на хладагентахR12 либо R-600, его нельзя заправлять R134а.
Возврат к списку